In the textile-care business the filtering of waste water performs major tasks. In the first place it removes foreign bodies from the liquor which, when re-using water flows, would be deposited on the goods. Since these undesired deposits always contain a larger proportion of lint, the industry is committed to minimising the particle discharge which comes in its own area of responsibility. This is successfully attained by a harmonisation of all components involved in the washing process. Texcare International will be showcasing the latest developments in this field, featuring new analysis methods, process guidelines and specialist filters.
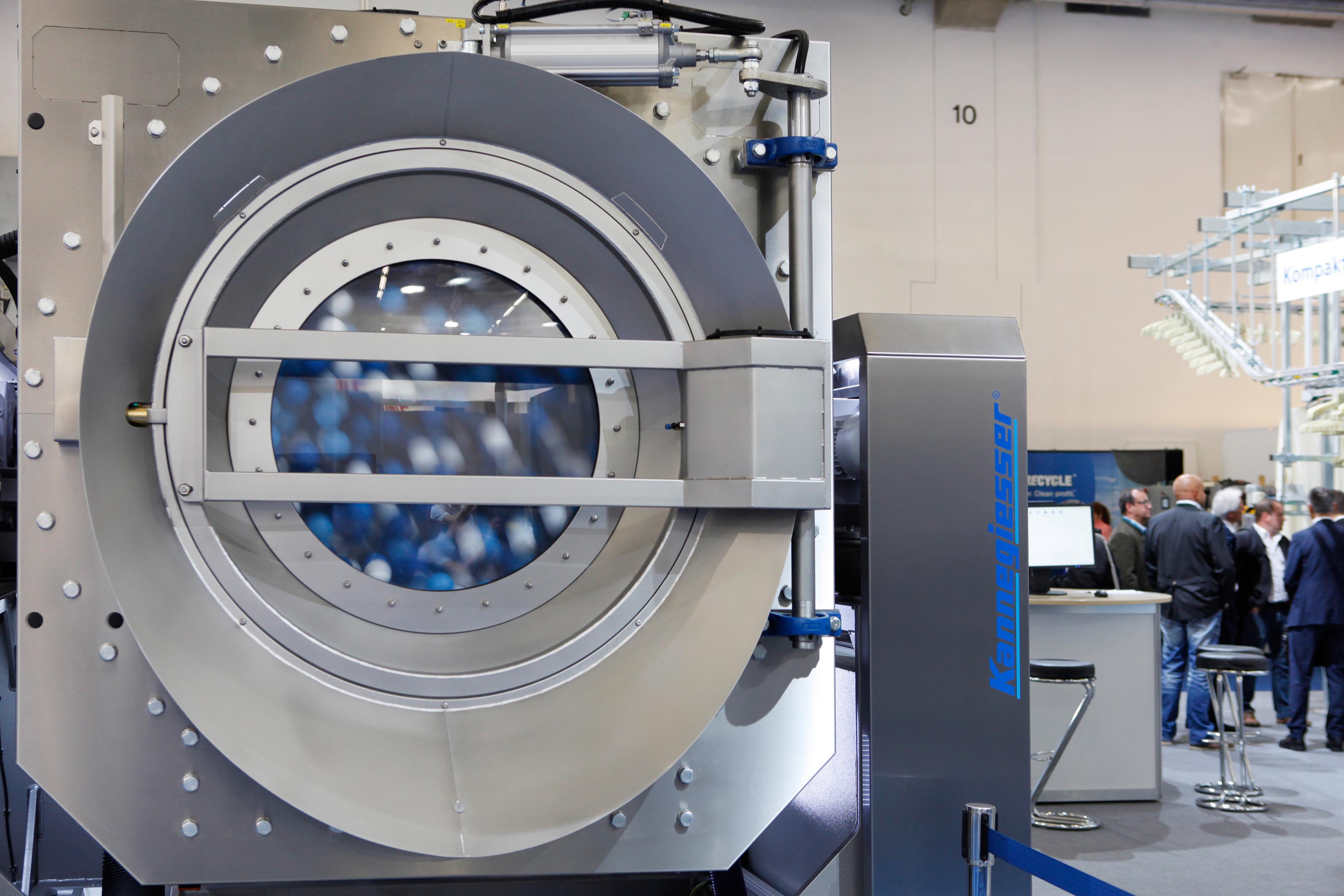
Along with the textiles for processing in a laundry come not just dirt of all kinds but also surface-adhering lint, hair and fibres into the washing liquor. They are detached in the washing process, flushed out and end up in a works collection tank or catch basin. In both systems this undesired mass has a disruptive effect: via the washing-water recycling process installed in the works, lint, dirt and related substances reach the laundry batches for processing again, where they are deposited on the textiles and are carried as a fine dust into the subsequent drying processes. In the waste water they impact in turn on the solids content, which in many countries is regulated through threshold values.
In laundries the problem of particles is solved by installing lint screens or filter systems. “Through a mechanical filtration of circulating water, the fluff, hairs and concomitant substances which have been released are captured and removed, by which means the washing quality rises significantly”, says Peter Zierler of ABZ Zierler in Bad Ischl, Austria. “Micro-revolving filters and sieves which use a filter supporting layer to ensure deep filtration have now enabled us to detach microscopically fine particles with a size of less than 50 micrometres. Given the current discussion about the environment, this system is becoming established more and more firmly in the textile-care industry, particularly since normal membrane processes such as microfiltration and ultrafiltration have major disadvantages in this fineness range: they tend to produce blockages, need resource-consuming flushing cycles to clean the membranes, and bring high costs for servicing and operation.” The mechanical filters adapted to the conditions of laundries, on the other hand, function smoothly even in the finest-particle ranges.
By the way: Of course, the current situation also raises the question of how to deal with waste water from laundry potentially contaminated with Corona viruses. The waste water does not need to be treated separately, as transmission by this route is considered unlikely. In addition, the viruses are inactivated in proper professional textile care with disinfecting laundering procedures. As a recent study published by the American Textile Rental Services Association (TRSA) shows, corona viruses are generally sensitive to temperature and washing chemistry.
Analysis methods make the tiniest particles visible
Even if the filtering of washing water leads to an effective particle separation, until now we have known little about the actual constituents. The industry is reliant on more precise data, however, in order for instance to promote the product development of low fluff and low lint textiles. “Thanks to dynamic image analysis, well-founded pronouncements have recently become possible about the concomitant components in milky-haze and coloured waste water”, senior scientific expert Dr Jan Beringer explains the process developed at Hohenstein Laboratories. “A representative portion of the liquor is pumped through a cuvette and passed by a camera. This takes a picture of each particle passing by the camera. The up to 10,000 pictures per analysis transit are then evaluated, using image-analysis software. In this way we can distinguish between particle-shaped and fibre-shaped solids in the waste water, identify the cellulose and synthetic percentage through a chemical separation process, and determine the number, length, diameter, length distribution and diameter distribution, the ‘curve’ and further parameters of the particles.” In this way businesses, for the first time, gain a comprehensive insight into the real conditions in their water, though the origin of the particles cannot be explained. Under laboratory conditions, however, even this question can be answered in part: using dynamic image analysis, the impact of washing parameters or textiles on fibre release can be compared. The results can then be adduced to establish a further optimisation of a washing process low in discharge.
Interplay of various factors
The textile-care industry is aware of its ecological responsibilities. To reduce the product-related fibre discharge to a minimum, rental-service companies have long been employing low-abrasion textiles, whose specialist construction additionally guarantees a long usage period. In future new washing aids will help to restrict synthetic microparticles in a liquor through encapsulation, aggregation or enzymic degradation. Moreover results of research are supplying further information about the impact of mechanical washing factors on the behaviour of textiles. From these can be derived new process parameters, such as loading and liquor ratios, by which abrasion and fibre discharge can be further reduced. Dry cleaning is also involved in reaching this goal. In contrast to household laundry, all textiles are treated very gently and any foreign bodies released are then removed from the solvents in the distillation system. The retained distillation sludge is then processed by specialist companies and the residue disposed of professionally.
Texcare International from 27 November to 1 December 2021 will address the numerous challenges facing the industry and will be showcasing across all sectors new concepts, products and processes, by which environmentally responsible textile care is harmonised with the industry’s very own commitments: conscientious cleanliness and reliable hygiene.