The productivity of a laundry depends on unbroken process flows and transparent commodity streams. Thanks to increasing digitalisation and consistent integration of data, the through-put of textiles in laundries is being continually improved. The solutions required for automation in the sector are therefore a high priority at Texcare International, from 27 November to 1 December in Frankfurt am Main.
The be-all and end-all for the laundry sector is the ability to monitor the quantity, quality and storage location of the textiles that are circulating on site, at all times. The data collected form the basis for precise price calculations, throw up any weak points in the system and serve to provide documentation for third parties. But it is only when all the machinery and plant involved in a given textile service are interlinked on a single network that the logistics of the laundry service run seamlessly, with minimal down-time of the machinery, reduced quantities in circulation and the resultant increase in productivity that is closely associated with it.
Transparent tracking for each individual laundry item
Automation in the processing of workwear is already well advanced. As the dirty laundry is sorted on arrival, each item is recorded using an identification system such as a barcode or RFID technology. From this moment on, all the stages that the textiles undergo are controlled. ‘Readers’ or ‘gates’ on the premises enable each item to be recorded as it progresses through the system, right up to the point of order picking; and they monitor whether an item is sent to a repair station or directed into storage. In addition, high-frequency transponders (UHF tags) can monitor the movements of laundry items outside of the laundry: in hospitals, for instance, identification systems have been installed, which record the despatch and return of apparel and enable an extensive process of textile management via data transfer procedures.
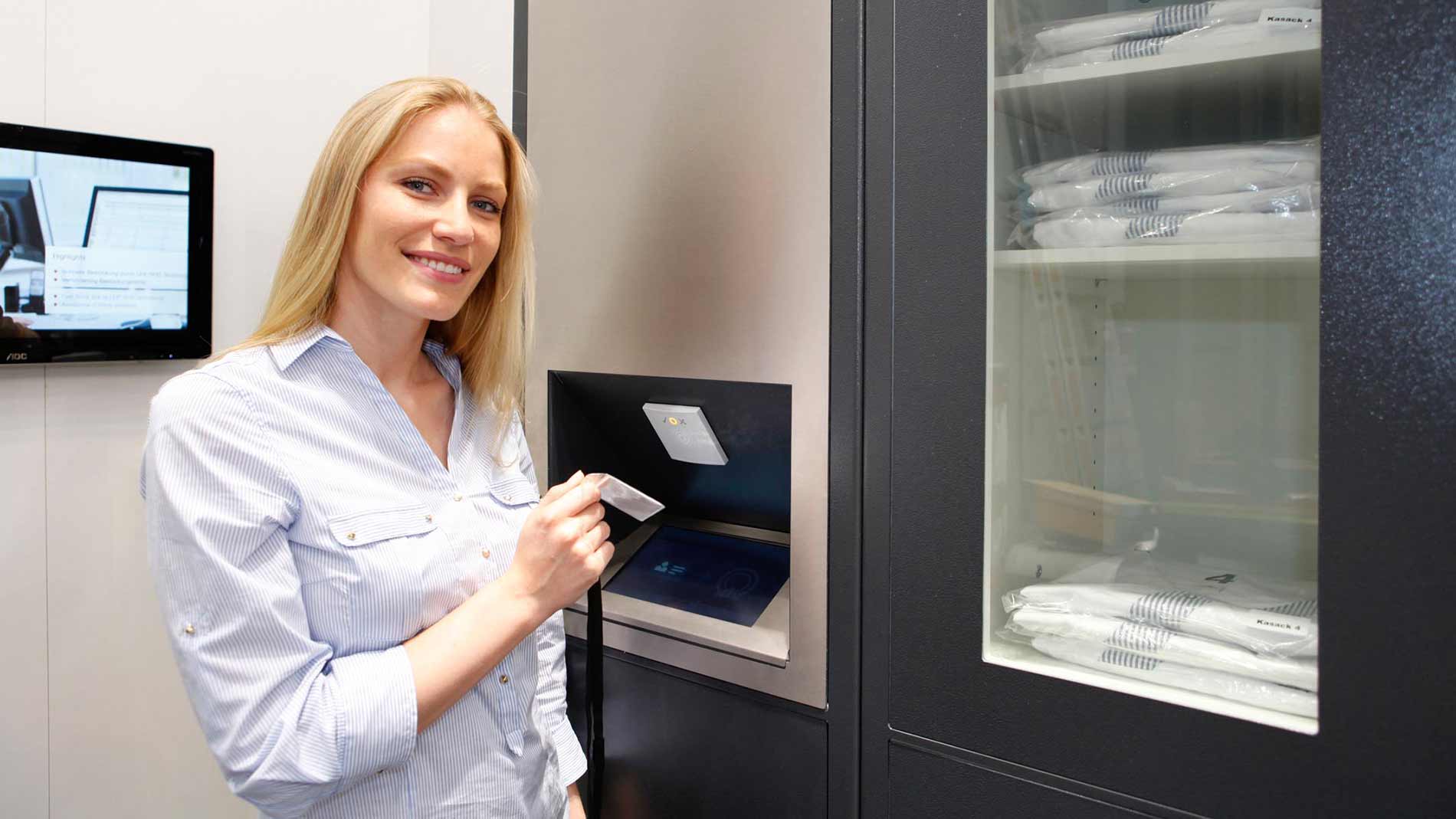
Robots for the soiled laundry area
This already high degree of automation in a workwear laundry facility is, however, capable of still further refinement. Artificial intelligence can simplify the ‘dirty’ work in the reception area: robots separate and sort the soiled clothing and x-ray machines, cameras and metal detectors are used to identify any foreign bodies. The advantages of such systems are particularly in evidence in hospital laundries: medical instruments, which regularly find their way into the laundry bags, are automatically separated from the clothing, thus minimising damage to the items themselves and to the machinery. The useful life of the textiles is extended and costs are reduced. Moreover, there is no danger of infection for the staff.
Real-time laundry processes
Whilst individual control and traceability are already widespread in the professional treatment of work apparel, when it comes to flat linen, often only generalisations about quantity, quality and storage location for the textiles are possible.
In the pursuit of automated production, ultra-modern information and communications technologies assume a key role. They synchronise the machines involved in a given production process and facilitate communication and cooperation between plant, product and the human being. This way, you get self-organising, flexible production with unbroken processes and high levels of utilisation of equipment. With the synchronisation of commodity streams and information flow in the laundry, all items arrive at the right processing station at the appropriate time. A central database controls all the processes in the entire laundry, regulates the machinery and the linked sub-systems, chooses the correct processing programmes and optimises machine use.
Data accompanies the laundry throughout
When data and goods flows are successfully synchronised throughout a flat-linen laundry, each washing station contributes its information along with that of other stations, right from the initial sorting of the soiled linen through to the folding machines. The laundry can, therefore, be monitored throughout the entire operation, as the information from each station is sent on with the item, either automatically or – after the drier – in the form of bar-coded labels. (“Stabilisation of production through the synchronisation of material and production flows.”) RFID identification systems do indeed enable complete transparency to be built into the passage of goods through the various stages, as each chip or tag carries the necessary information for each individual item. In view of the high cost of the transponders, ‘chipping’ of flat linen is, however, currently an option for only very few laundries. So the textile care sector is waiting on more economical, more functionally reliable solutions from the machinery and plant manufacturers.
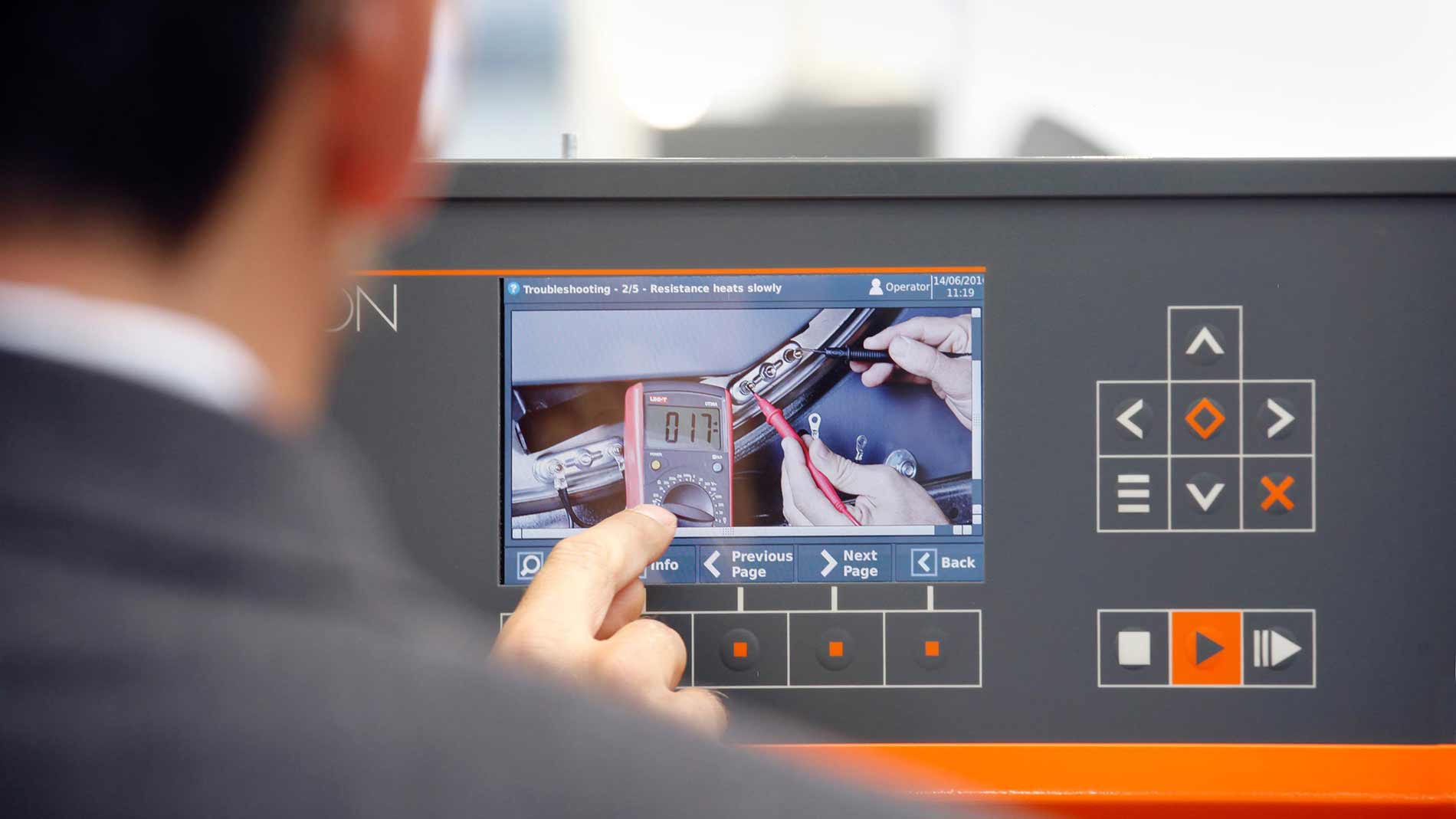
Smart to the very end of the chain
Further potential for automation resides in the picking and packaging. Collecting together items for delivery manually is subject to error and that leads to customer complaints. With intelligent storage facilities and transport solutions, smart stacking management and the networking of equipment with the laundry’s information system, order picking becomes simpler, quicker and more reliable. To ensure that the integration can function, modern machines are equipped with interfaces, so that each new installation can be linked seamlessly into a laundry’s existing system. The same goes for accessory machines, which exchange all the important information relating to preparation and repair online.
User friendly apps
Digital developments are not only large scale: they are to be found on a smaller scale as well. For launderettes, too, apps provide important information on the status of the equipment, enable operators to see what is going on, even at considerable distances, as well as being able to provide digital payment models.